Protecting the environment and creating a recycling-oriented society
The Ariake Group is committed to promoting environmental protection and creating a recycling-oriented society at all stages of the production process. This is in line with company's code of behavior, which stipulates that we shall "strive to reduce the environmental impact of our operations in order to preserve the global environment and promote establishing a recycling-based society." As part of this commitment the Ariake Group has set out a range of voluntary environmental targets and objectives in line with the procedural requirements of ISO14001.
(1) Environmental principles
Ariake will contribute to the society with our basic principle of the harmony between the natural seasoning business and the preservation of global environment.
- Ariake will promote our operation in every section with less energy, less resources, recycling and less waste.
- Ariake will provide environment friendly products.
- Ariake will set up the environment target and make the best efforts to attain it through the continual improvement.
- Ariake will try best to prevent the pollution complying with relevant laws, regulations and other appropriate requirements.
- Ariake will announce this policy to the public as well as to all the employees and everyone who works for Ariake and call their attention to the environment.
Based on the Company' s four basic themes, "Natural," "Healthy," "Safety," and "Convenience," we are actively involved in environmental issues.
(2) Product development
A key environmental initiative at the Ariake Group is the shift to aseptic production with rapid high-temperature sterilization. Aseptic production is more energy-efficient than conventional cans and retort pouches, while delivering quality standards equivalent to frozen products without the need for freezing. It also generates cost savings in storage and transportation, thus reducing energy usage and associated CO2 emissions. And finally, it extends the "best before" period, which helps to reduce expired product wastage at the warehousing stage.
(3) Manufacturing
- Effective use of residue
The No. 2 Kyushu Plant is committed to creating a recycling-oriented society. Part of the residue occurring after extracting bouillon in the manufacturing process is externally composted and reused, with 4,400 t of residue externally reused as compost in FY2018 (the fiscal year ended in March 2019).
- Effective use of resources
ARIAKE JAPAN Co., Ltd. procures livestock carcasses as ingredients and uses them effectively in the form of extracts when producing seasonings, soups and other focus products. In this way, we engage in initiatives at the core of our business activities to achieve a recycling-oriented society.
- Waste energy harvesting
The No. 2 Kyushu Plant strives to reuse energy resources. For example, waste heat and waste oil are harvested and reused to run the boilers, while wastewater such as coolant is also reused wherever possible. Also, waste oil remaining after the bouillon extraction process is collected and reused as fuel externally, with 151 t of waste oil reused in FY2018.
Additionally, sludge is collected from wastewater treatment facilities and oil harvested from this sludge in an external operation is reused as fuel, with 990 t of sludge reused in FY2018.
In these ways, the plant is also committed to creating a recycling-oriented society through initiatives to reuse energy resources.
- Natural energy
Solar panels installed on the roof of the No. 2 Kyushu Plant generate natural energy for factory operations. In addition, we are participating in verification tests for next-generation recycling-oriented farming initiatives that utilize solar power generation without resorting to fossil fuels at the reclaimed land of Isahaya Bay.
- Reducing greenhouse gas emissions
ARIAKE JAPAN Co., Ltd. is working to minimize greenhouse gas emissions associated with our operations via the following initiatives:
- Detection and prompt repair of steam leaks
- Installing thermal insulation around steam pipes, joints and fittings
- Replacing mercury vapor lamps and fluorescent tubes with LED light fittings
The actual unit greenhouse gas output (output per unit production) was 803.3 t-CO2 per unit production in FY2017 (the fiscal year ended in March 2018) and 754.7 t-CO2 per unit production in FY2018. As such, we are reducing output levels at a favorable pace.
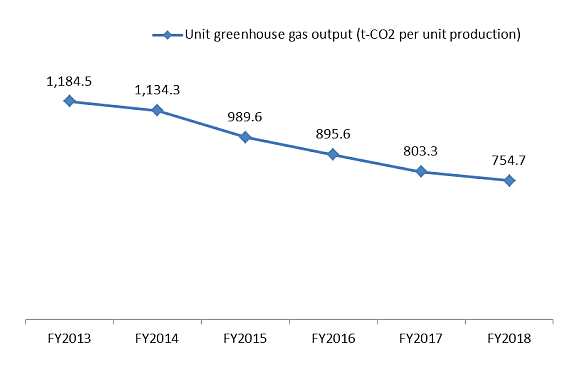
- Reducing emissions and waste
The No. 2 Kyushu Plant makes thorough efforts to reduce the amount of wastewater, exhaust gases, waste heat, waste oil, industrial waste and food waste generated in the manufacturing process.